Frequently Asked Questions
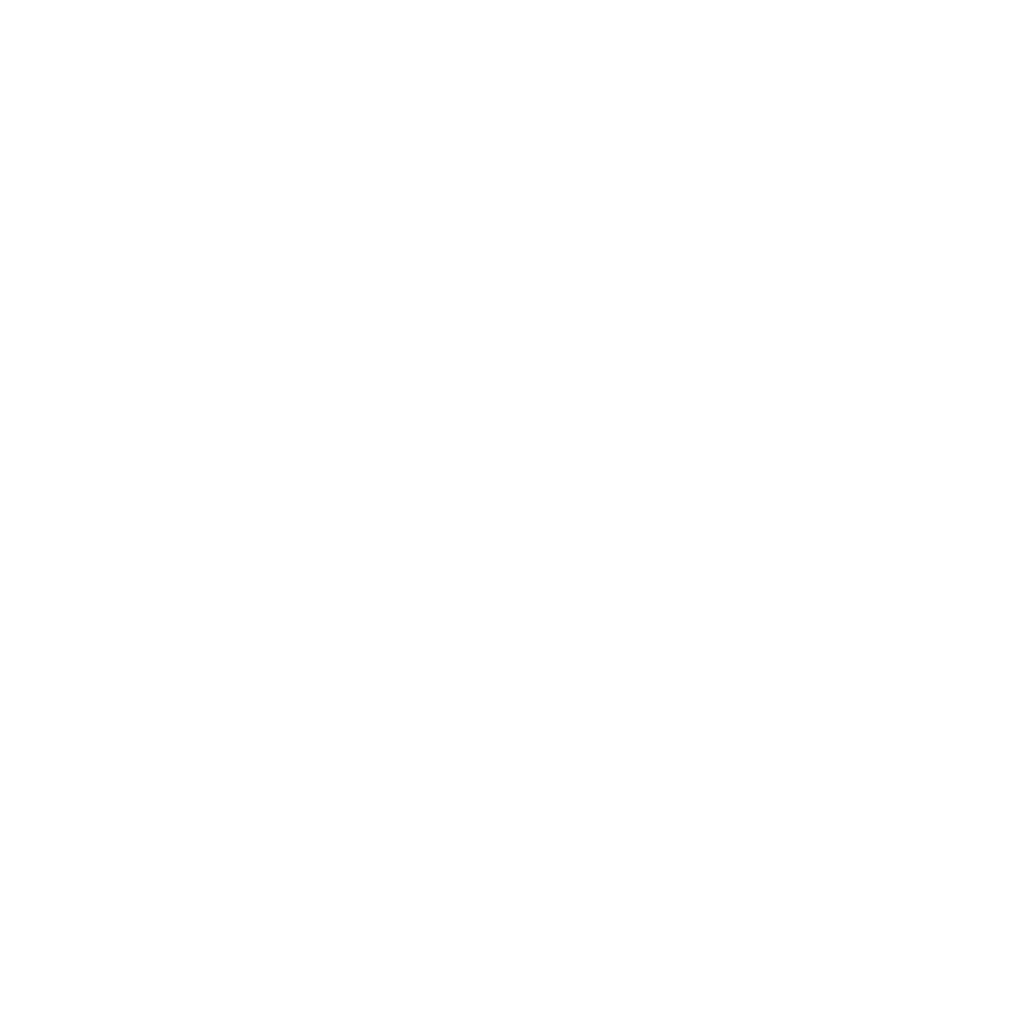
Support Email
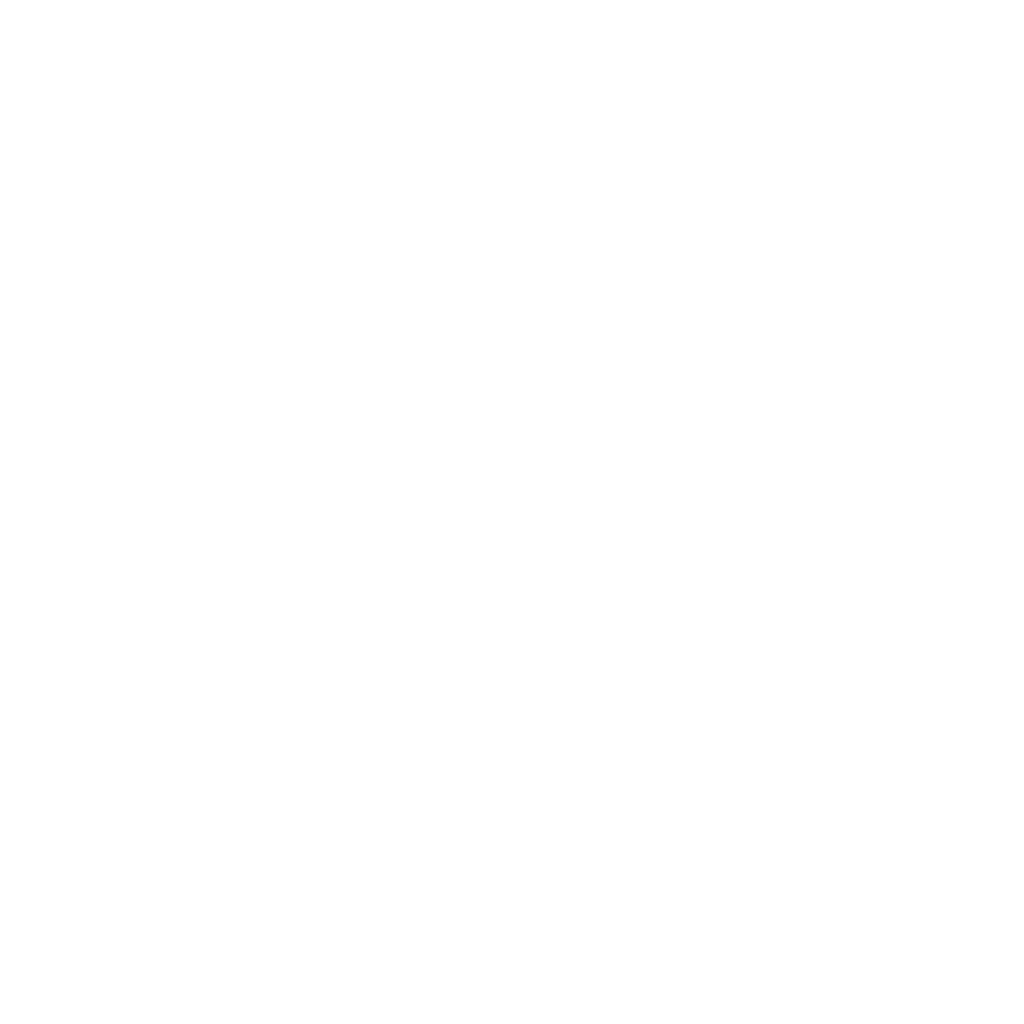
Support Phone
1-866-493-0524
Check the most frequently asked questions here, if you still need help then please use the contact us options on the homepage.
Returns
Return/Refund Policy
We have a 30-day return policy, which means you have 30 days after receiving your item to request a return.
To be eligible for a return, your item must be in the same condition that you received it, unworn or unused, with tags, and in its original packaging. You'll also need the receipt or proof of purchase.
How to File a Return
To initiate a return, please fill out the "Contact Us" form on our GCM Product Support Help Center. Provide your order number, reason for return, and any relevant details. Our customer support team will review your request and guide you through the next steps.
Gas-Powered Products
Due to hazmat concerns, gas-powered products (including those that use gas or oil) cannot be returned once operated (i.e., filled with gas or oil). These items must be in unused condition to be eligible for return.
If your return is accepted, we’ll send you a return shipping label, as well as instructions on how and where to send your package. Items sent back to us without first requesting a return will not be accepted. Please note that if your country of residence is not the United States, shipping your goods may take longer than expected.
Restocking Fee for Buyer's Remorse - Starting 10/24/23
If you're returning the item for reasons of buyer's remorse, please note that a 15% restocking fee will be deducted from your refund. The item must be unused and in its original packaging. If the items are shown to be used upon inspection, your refund could be denied.
Get Free Returns via Buy with Prime
Want to truly maximize your shopping benefits with us? Choose the "Buy with Prime" option at checkout for a hassle-free, 30-day return period without any restocking fees. Note: free shipping is a standard feature we proudly offer on all orders. Opting for the "Buy with Prime" checkout guarantees free returns. Choosing otherwise subjects your return to the standard 15% restocking fee for buyer's remorse.
Damages & Defects
Inspect your order upon reception and contact us immediately if the item is defective, damaged, or if you receive the wrong item, allowing us to promptly address the issue.
Final Sale Items
Some products are not available for return or refund unless they're received in a defective or damaged state. Such products typically include, but aren't limited to, Clearance, Refurbished/Pre-Owned, and Discontinued items. They will be clearly marked as "Final Sale" on their listings. Ensure you're confident about your purchase decisions concerning these products.
Exchanges
For the quickest resolution, return the item you have, and after the return is accepted, place a new order for the desired item.
Refunds
We'll notify you once we've reviewed and inspected your return, informing you if the refund is approved. If so, expect the refund to reflect on your original payment method within 10 business days. Remember, it might take additional time for your bank or credit card company to process and post the refund. If over 15 business days have passed since your return was approved and you've not received your refund, please reach out to us through the "Contact Us" form on our GCM Product Support Help Center.
It is generally recommended to avoid including items from multiple orders or shipments in the same return package. Each return label is typically assigned to a specific return and is associated with a particular order. To ensure accurate and efficient processing of your returns and refunds, it is best to separate the items by order and package them accordingly.
Returning items separately for each order allows for better tracking and identification of the returned items, ensuring that the correct refund or exchange is provided for each specific order. It also helps streamline the processing and verification of returns, minimizing any potential confusion or delays.
If you need to return items from multiple orders, we suggest packaging them individually and attaching the respective return labels provided for each order. This will help maintain clarity and accuracy throughout the return process, ensuring that each order is handled appropriately.
If you have any questions or concerns regarding the return of multiple orders or need further assistance, we recommend reaching out to our customer support team. They will be able to provide you with specific guidance and address any queries you may have regarding your particular situation.
Customer Responsibility for Non-Defective Returns: If you decide to return an item for reasons other than it being defective, damaged, or incorrect, you will be responsible for the return label fees. Please note that the return label fees will be deducted from your refund.
Shipping
This website is our United States store, we do not ship to P.O. Boxes, Puerto Rico, or Alaska addresses.
For Canada see: www.greatcircleca.com
For the United Kingdom see: www.greatcircleus-uk.com
For Germany see: www.greatcirclede.com
The typical processing time for orders is 1-3 business days. During this period, our team works diligently to process and prepare your order for shipment. Please note that this processing time does not include weekends or holidays.
Once your order is ready to be shipped, we utilize reliable shipping carriers such as UPS Ground, USPS Priority, or FedEx Ground to deliver your package. The shipping times may vary depending on the destination, the specific carrier service chosen, and external factors beyond our control.
To obtain a more accurate estimate of the shipping time for your order, we recommend referring to the tracking information provided via email once your order has been shipped. This tracking information will allow you to monitor the progress of your shipment and provide you with a better understanding of its expected delivery timeframe.
If you have any specific inquiries or concerns regarding the shipping of your order, we encourage you to reach out to our customer support team. They will be happy to assist you and provide further information based on your individual circumstances and location.
Please note that while we strive to ensure timely delivery, unforeseen circumstances such as weather conditions or logistical issues may occasionally impact the delivery timeframe. We appreciate your understanding in such situations and assure you that we will make every effort to ensure a smooth shipping experience for your order.
We will handle all taxes and duties. Please order from the appropriate store.
For Canada see: www.greatcircleca.com
For the United Kingdom see: www.greatcircleus-uk.com
For Germany see: www.greatcirclede.com
Product Manuals
These can typically be found on the product page on this website under the description. If you are unable to locate it there, try searching for the manual at this link Here
If you cannot locate them on either front, please contact support and they will be able to provide you with the appropriate documentation.
Orders from greatcircleus.com
To check the status of your order on Shopify, please follow these steps:
1. Check your email: After placing an order on Shopify, you should receive an email confirmation. This email contains important details about your order, including a tracking link or information.
2. Open the order confirmation email: Locate the order confirmation email in your inbox. It is usually sent from the store or seller you made the purchase from.
3. Click on the tracking link: Within the order confirmation email, you will find a button or link specifically labeled for tracking your order. Click on this tracking link to be directed to the tracking page.
4. Track your order: The tracking page will provide you with real-time updates on the status and progress of your order. You will be able to see information such as the current location of the package and estimated delivery dates.
If you cannot locate the order confirmation email in your inbox, make sure to check your spam or junk folder as it might have been filtered there. If you are still unable to find the email or encounter any issues, it is recommended to reach out to the store or seller directly through their contact information provided on the Shopify website. They will be able to assist you in tracking the status of your order or provide you with the necessary information.
Please note that the tracking link and tracking process may vary depending on the specific store or seller on Shopify. It is always best to refer to the order confirmation email for the most accurate and up-to-date tracking information.
Once an order is placed, it is not possible to make changes to the order. However, there are certain circumstances in which modifications may be allowed. If the item has not yet been shipped and it will not be fulfilled by MCF, there might be a possibility to update the shipping address. Please reach out to our customer support team as soon as possible with your order details to inquire about the feasibility of updating the shipping address.
To return an item purchased from our Shopify website, please follow these steps:
1. Review the eligibility criteria: Most orders, excluding clearance and refurbished/used items, are eligible for return within 30 days of receiving the item. To be eligible for a return, the item must be unused and in the same condition as when you received it. It should also be in its original packaging.
2. Gather required information: To complete your return, please ensure you have the receipt or proof of purchase handy. This can be in the form of the order ID or order number, which helps us locate your purchase in our system.
3. Avoid returning directly to the manufacturer: Please note that returns should not be sent back to the manufacturer. Follow the instructions provided to ensure a smooth return process.
4. Fill out the return request: To initiate the return process, please visit our return request page at [Return Request Form](https://greatcircleus.com/pages/return-requests). This form will allow you to provide the necessary details, including your contact information, order details, and reason for the return.
5. Await return label (if applicable): If your order is eligible for a return, you will receive a return label to facilitate the return shipment of the unwanted item. This label helps ensure the return is properly tracked and received.
6. Ship the item back: Once you receive the return label, securely package the item and attach the provided return label to the package. Ship it back to us using a reliable shipping method. If the return label is not provided, please follow the specific return instructions provided in the return request confirmation.
7. Verification and refund processing: Once we receive the returned item, our team will verify its condition and completeness. After verification, a refund will be processed to your original payment method. Please note that refund processing times may vary depending on your payment provider.
We appreciate your cooperation in adhering to the return process outlined above. If you have any further questions or require assistance regarding your return, please reach out to our customer support team. We're here to help ensure a seamless return experience for you.
Orders from Amazon
To check the status of an order placed on Amazon, please follow these steps:
-
Log in to your Amazon account: Visit the Amazon website and log in using the same account you used to place the order.
-
Go to "Your Orders" page: Once logged in, hover over the "Accounts & Lists" tab located at the top right corner of the page. From the drop-down menu, select "Your Orders."
-
Locate your order: On the "Your Orders" page, you will see a list of your recent orders. Find the specific order you would like to check the status of and click on it to open the order details.
-
Review order details: In the order details section, you will find information such as the estimated delivery date, shipping carrier, and any available tracking information. This will give you an idea of the current status and whereabouts of your order.
-
Track your order: If tracking information is available, you will see a tracking number or a link to track your package. Click on the tracking number or the provided link to access the tracking details and get real-time updates on the status and location of your order.
-
Contact customer support, if needed: If you have further questions or concerns about your order's status, or if you don't see any tracking information available, you can reach out to Amazon's customer support team for assistance. They will be able to provide you with more specific information and address any inquiries you may have.
It's important to note that the availability of tracking information and the level of detail may vary depending on the shipping method, carrier, and the specific products you ordered. If your order does not have tracking information or if you have any additional questions, contacting Amazon's customer support is the best way to get accurate and up-to-date information regarding the status of your order.
Once an order is placed, it is not possible to make changes to the order. However, there are certain circumstances in which modifications may be allowed. If the item has not yet been shipped and it will not be fulfilled by Amazon, there might be a possibility to update the shipping address. Please reach out to our customer support team as soon as possible with your order details to inquire about the feasibility of updating the shipping address.
If you made a purchase through Amazon, please follow these steps to initiate a return:
-
Access your Amazon account: Log in to your Amazon account and navigate to the "Your Orders" section.
-
Locate the order: Find the order containing the item you want to return and select the "Return or Replace Items" option.
-
Choose the item and reason for return: Select the specific item you wish to return from the order and indicate the reason for the return. You may be asked to provide additional details about the return, such as whether the item is defective or if you simply changed your mind.
-
Select return method: Choose the preferred return method based on the options provided by Amazon. This could include self-return, where you package and ship the item yourself, or in some cases, Amazon may offer a prepaid return label for convenience.
-
Package the item: Carefully pack the item in its original packaging, including any accessories, documentation, or promotional items that came with it. Ensure the item is well protected during transit.
-
Attach the return label: If Amazon has provided a prepaid return label, affix it to the package. If not, follow the instructions provided by Amazon for self-return, including the return address and any necessary shipping instructions.
-
Ship the package: Use a reliable shipping method to send the package back to Amazon. If a prepaid return label was provided, follow the specific instructions for drop-off or scheduling a pickup. For self-return, consider using a trackable shipping service to ensure the safe delivery of the item.
-
Await confirmation and refund: Once Amazon receives and processes your return, they will notify you via email. The refund will be issued to your original payment method. You can track the status of your return through your Amazon account.
It's important to note that the specific steps and options for returns may vary depending on Amazon's policies and the nature of the item being returned. For any further assistance or clarification, we recommend reaching out to Amazon's customer support team directly or consulting their return policy for more detailed instructions.
Orders from Walmart
Once an order is placed, it is not possible to make changes to the order. However, there are certain circumstances in which modifications may be allowed. If the item has not yet been shipped and it will not be fulfilled by MCF, there might be a possibility to update the shipping address. Please reach out to our customer support team as soon as possible with your order details to inquire about the feasibility of updating the shipping address.
To check the status of your order from Walmart, you can follow these steps:
1. Visit the Walmart website: Go to the official Walmart website using your preferred web browser.
2. Navigate to the "Orders" section: On the Walmart homepage, locate the "Account" or "Sign In" option, usually located at the top right corner of the page. Click on it to access your Walmart account.
3. Sign in to your Walmart account: Enter your login credentials, including your email address and password, to sign in to your Walmart account. If you don't have an account, you may need to create one using the same email address you used to place your order.
4. Go to the "Orders" page: Once you are logged in, navigate to the "Orders" or "Order History" section. This section typically contains information about your past and current orders.
5. Locate your order: Look for the specific order you want to check the status of. You can often find orders listed by their order number, date, or item details.
6. Click on the order details: Click on the order you wish to track to access the detailed information.
7. Review the order status: Within the order details page, you should be able to see the current status of your order, such as "Processing," "Shipped," or "Delivered." Additionally, you may find tracking information, estimated delivery dates, and any available updates related to your order.
For further convenience, you can directly access the Walmart Orders page by visiting the following link: [Walmart Orders](https://www.walmart.com/orders)
If you have any questions or concerns about the status of your order or if you require more specific information, you can reach out to Walmart's customer support for assistance. They will be able to provide you with accurate and up-to-date information regarding the status and progress of your Walmart order.
To return an item purchased on Walmart.com, you can follow these steps:
1. Review Walmart's return policy: Before initiating a return, it's recommended to familiarize yourself with Walmart's return policy. This policy outlines the eligibility criteria, time limits, and any specific requirements for returning items.
2. Prepare the item for return: Ensure the item you wish to return is in its original condition and packaging, including any accessories, manuals, or tags that came with it. This helps facilitate the return process.
3. Initiate the return online: Visit the Walmart website and sign in to your Walmart account. Navigate to the "Account" or "Orders" section, where you should find a list of your recent orders. Locate the specific order containing the item you want to return and select the "Return" or "Start a Return" option next to it.
4. Choose the return method: Walmart provides various options for returning items, including returning items to a Walmart store or initiating a return by mail. Select the return method that is most convenient for you.
5. Follow the return instructions: Walmart will guide you through the return process based on the chosen return method. If returning to a store, you may need to generate a return barcode or print a return label. If returning by mail, you will receive instructions on how to package the item and where to send it.
6. Ship or bring the item to Walmart: If you chose to return the item to a store, package the item securely and take it to the specified Walmart store. Present the return barcode to a Walmart associate, who will assist you with the return process. If returning by mail, affix the provided return label to the package and ship it to the designated address.
7. Track the return (if applicable): If you returned the item by mail, you may want to track the shipment to ensure it reaches Walmart successfully. Follow the provided tracking information or contact the shipping carrier for updates.
8. Await refund or exchange: Once Walmart receives and processes your returned item, they will issue a refund to your original payment method or provide an exchange, depending on your preference and the item's condition. The refund processing time may vary based on the payment method and bank processing times.
If you have any questions or encounter any issues during the return process, Walmart's customer support team is available to assist you. You can reach out to them for further guidance or clarification regarding your specific return.
Charging My Battery
The charging times for different battery types and voltage levels are as follows:
48 VOLT LEAD ACID: It generally takes approximately 3-4 hours to charge a 48V lead acid battery. This charging time applies to products such as GUO010.
24 VOLT LEAD ACID: Charging a 24V lead acid battery typically takes around 2-3 hours. This applies to products like GUO041, GUO073, GUO032, and GUO034.
48 VOLT LITHIUM ION: For a 48V lithium-ion battery, the charging time is generally 2-3 hours. This applies to various products, including GUO057, GUO055, GUO026, GUT112, GUT121, GUO046, GUO048, GUO082, GUO058, GUT071, GUO069, GUO061, GUO043, GUO037, GUO075, and GUO036.
20 VOLT LITHIUM ION: Charging a 20V lithium-ion battery typically takes about 1-2 hours. This applies to products such as GUT057, GUT062, GUT063, GUT099, GUT100, GUT036, and GUT085.
It's important to note that these charging times are approximate estimates and can vary depending on the specific battery model, charger specifications, and environmental conditions. It is advisable to refer to the manufacturer's instructions or documentation provided with your specific battery or device for precise charging time recommendations.
Properly following the recommended charging times helps ensure efficient charging and optimal performance of the battery. Overcharging or undercharging can negatively impact the battery's lifespan and overall functionality.
Battery Replacements
Please refer to your Product current/rated battery voltage and select one of the following battery options:
20V
2Ah : Buy Here
4Ah : Buy Here
48V
2Ah : Buy Here
4Ah : Buy Here (Note some products are not compatible as they do not fit in the slot i.e Mobility Scooter will not work with the 4Ah battery)
24V Lead Acid AGM (2 - 12V AGM Batteries)
To properly maintain a lithium-ion (Li-ion) battery, follow these guidelines:
1. Avoid extreme temperatures: Li-ion batteries perform best within a specific temperature range. Avoid exposing the battery to extreme heat or cold, as it can degrade its performance and lifespan. Optimal temperature range for most Li-ion batteries is between 20°C (68°F) and 25°C (77°F).
2. Charge regularly: Li-ion batteries work best when they are regularly charged. Avoid letting the battery fully discharge before recharging. It is recommended to keep the battery charged between 20% and 80% capacity for optimal performance.
3. Use an appropriate charger: Always use a charger specifically designed for Li-ion batteries and recommended by the manufacturer. Using an incompatible or low-quality charger can damage the battery and reduce its lifespan.
4. Avoid overcharging: Once the battery reaches its full charge, unplug it from the charger. Overcharging can cause stress on the battery and lead to reduced capacity over time.
5. Store at appropriate charge level: If you need to store the Li-ion battery for an extended period, ensure it is stored with a charge level between 40% and 60%. Storing the battery at full charge or very low charge for a prolonged period can lead to capacity loss.
6. Keep the contacts clean: Regularly check the battery contacts for any dirt, dust, or corrosion. If necessary, clean the contacts using a soft, dry cloth. This helps maintain a good electrical connection between the battery and the device.
7. Protect from physical damage: Avoid dropping, crushing, or subjecting the Li-ion battery to excessive physical force. Physical damage can compromise the battery's safety and performance.
8. Replace when necessary: Li-ion batteries have a limited lifespan. If you notice a significant decrease in battery capacity, reduced runtime, or the battery fails to hold a charge effectively, it may be time to consider replacing the battery.
Following these maintenance practices will help maximize the lifespan and performance of your Li-ion battery. However, it is essential to consult the specific guidelines provided by the battery manufacturer for your device, as there may be additional recommendations or precautions to consider.
Charger Replacements
48V Lead Acid Charger - Compatible SKUS: GUO010
24V Lead Acid Charger - Compatible SKUS: GUO041, GUO073
24V Lead Acid Charger - Compatible SKUS: GUO032, GUO034
48V Li-Ion Charger - Compatible SKUS: GUO057, GUO055, GUO026, GUT112, GUT121, GUO046, GUO048, GUO082, GUO058, GUT071, GUO069, GUO061, GUO043, GUO037, GUO075, GUO036
20V Li-Ion Charger - Compatible SKUS: GUT057, GUT062, GUT063, GUT099, GUT100, GUT036, GUT085
Log Splitters
Unfortunately, if the ram is bent or there is hydraulic fluid leaking from the shaft, it indicates a problem with the hydraulic cylinder. To resolve this issue, you will need to replace the hydraulic cylinder. We recommend contacting our customer support for further assistance in this matter.
If your equipment is still within the one-year period from the date of purchase, the replacement parts required for fixing the hydraulic cylinder will be provided free of charge. However, if the equipment is outside of this warranty period, you will be expected to purchase the replacement part.
Our customer support team will be able to guide you through the process of obtaining a replacement hydraulic cylinder and assist you with any additional steps or instructions required for the replacement.
Please reach out to our customer support as soon as possible to address this issue and ensure your equipment is back in proper working condition.
If your motor is humming but the ram does not move, it indicates a potential issue with either the motor or the pump. To diagnose the problem, we recommend following these steps:
-
Disconnect the pump: Start by disconnecting the pump from the motor. This involves detaching any connecting hoses or belts between the motor and the pump.
-
Test the motor: After disconnecting the pump, turn on the log splitter. If the motor runs fine without the pump attached and the humming noise disappears, it suggests that the pump is faulty and needs to be replaced.
-
Replacement motor: However, if the motor continues to hum and does not operate properly even without the pump connected, it indicates a problem with the motor itself. In this case, you will need to replace the motor to restore the functionality of your log splitter.
We recommend contacting our customer support for further assistance in obtaining a replacement motor or pump, depending on the diagnostic results. They will be able to guide you through the process and provide you with the necessary information and instructions.
For your log splitter, it is recommended to use Hydraulic Oil AW-32. AW-32 is a common type of hydraulic oil with specific properties suitable for various hydraulic systems, including log splitters.
When adding hydraulic oil to your log splitter, follow the manufacturer's instructions regarding the proper oil fill level and any recommended maintenance procedures. These can be found in your operator's manual which should have come with the product. If not you should be able to find a download on the product page on our website.
There is an adjustment knob located underneath a cap on the pump itself. To resolve the issue, rotate the knob 180 degrees clockwise.
Mobility Scooters
The weight capacity for your scooter depends on the specific model. Here's a recommended answer:
For the basic models GUT112 and GUT142, the weight capacity is 275 lbs (125 kg). These models are designed to safely support individuals weighing up to 275 lbs.
For the plus models GUT140 and GUT121, the weight capacity is 330 lbs (150 kg). These models are specifically built to accommodate individuals weighing up to 330 lbs.
It's important to adhere to the weight capacity guidelines to ensure safe operation and optimal performance of your scooter. Exceeding the recommended weight capacity may compromise the scooter's stability and functionality.
If you have any further questions or need more specific information about the weight capacity of your particular scooter model, we recommend referring to the scooter's manual or contacting our customer support team for accurate and detailed specifications.
The difference between the basic and plus model scooters can be summarized as follows:
Basic Models: (GUT112 & GUT142)
- Seat: The basic models have a less cushioned seat compared to the plus models.
- Arm rests: The basic models do not come with arm rests.
- Adjustable tilt handlebars: The basic models do not have adjustable tilt handlebars.
- Ground clearance: Basic models are slightly lower to the ground.
- Wheels: The basic models typically come with smaller 6" wheels.
Plus Models: (GUT140 & GUT121)
- Seat: Plus models feature a more cushioned seat for enhanced comfort.
- Armrests: Plus models come with armrests for additional support and comfort.
- Adjustable tilt handlebars: Plus models have adjustable tilt handlebars, allowing users to customize the handlebar position according to their preferences.
- Ground clearance: Plus models may have a slightly higher ground clearance compared to the basic models.
- Wheels: Plus models are equipped with larger 8" wheels, which can provide improved stability and maneuverability.
Additionally, the plus models often have a reinforced frame design to support a higher weight capacity of 330 lbs, providing added strength and durability.
These differences in features and specifications allow users to choose a model that best suits their preferences and requirements. It is important to carefully consider these distinctions when selecting a scooter model that meets your specific needs.
For more detailed information about the features and specifications of each model, we recommend referring to the product descriptions or reaching out to our customer support team for further assistance.
The round black part on the left handlebar of your scooter is a standard bicycle bell. Its purpose is to alert pedestrians or other individuals of your presence and to ensure safer navigation in shared spaces.
Yes, it is generally safe and possible to take your mobility scooter on an airplane. However, there are specific guidelines and regulations that need to be followed, primarily related to the transportation of the scooter's battery.
To ensure compliance and safety, it is typically required to remove the battery from the mobility scooter and transport it in your carry-on bag. This is because batteries are considered hazardous materials and are subject to specific rules for air travel.
Here are some general steps to follow when taking your mobility scooter on an airplane:
-
Check airline policies: Before your flight, review the policies and guidelines of the airline you are traveling with regarding the transportation of mobility scooters. Each airline may have its own specific regulations and requirements.
-
Remove the battery: Disconnect the battery from the mobility scooter following the manufacturer's instructions. In most cases, the battery needs to be transported separately in your carry-on baggage.
-
Secure the battery: Place the battery in a protective case or wrap it in appropriate packaging to prevent damage or accidental activation during transportation. Ensure that it is well-secured to avoid any movement or contact with other items in your carry-on bag.
-
Inform the airline: It is advisable to inform the airline in advance about your intention to travel with a mobility scooter. They may require additional documentation or provide specific instructions on how to handle the scooter and battery during check-in and boarding processes.
-
Follow security procedures: When going through security checkpoints, be prepared to present the battery separately for screening, following the guidelines provided by the airport security personnel.
It is important to note that regulations and requirements may vary among airlines and countries. It is recommended to check with your specific airline and consult their official guidelines or contact their customer support for the most accurate and up-to-date information regarding traveling with a mobility scooter on their flights.
The first step in tightening or performing maintenance on your scooter's brake is to adjust the cable tensioner located at the handlebars. Here's how you can do it:
-
Locate the cable tensioner: Identify the cable tensioner mechanism on your scooter's handlebars. It is usually a small knob or lever that allows you to adjust the tension of the brake cable.
-
Tighten the cable tensioner: Turn the knob or lever clockwise to tighten the brake cable. This will increase the tension on the cable and can help improve the braking performance.
-
Test the brakes: After tightening the cable tensioner, test the brakes by squeezing the brake lever on the handlebars. Ensure that the brakes engage properly and provide the desired stopping power. If the brakes still feel loose or inadequate, further adjustment may be required.
If tightening the cable tensioner does not resolve the brake issue, you can proceed to the next step, which involves tightening the nut on the back drive wheel. Here's how:
-
Locate the nut: Find the nut on the back drive wheel that is connected to the black lever.
-
Compress the lever: Use a wrench or the appropriate tool to twist the nut clockwise, compressing the black lever connected to it. This action will increase the tension on the brake system and make it tighter.
-
Adjust to desired tightness: Twist the nut until you achieve the desired tightness for the brakes. Be cautious not to overtighten, as it may cause the brakes to drag or malfunction.
It's important to note that brake systems may vary among different scooter models, so the specific steps and mechanisms involved in brake maintenance may differ. Always refer to the manufacturer's instructions and guidelines provided in the scooter's manual for accurate information on maintaining and adjusting the brakes.
If you are unsure about performing brake maintenance or encounter any difficulties, it is recommended to seek assistance from a qualified technician or contact the scooter's manufacturer or customer support for further guidance.
To troubleshoot and resolve the issue with your mobility scooter not working, please follow these steps:
-
Check the brake lever: Ensure that the brake lever is in the open or released position. Some mobility scooters have a safety feature that prevents the scooter from moving when the brake lever is engaged.
-
Verify the on/off switch: Make sure that the on/off switch is in the "on" position. This switch is usually located on the control panel or near the handlebars. If it is in the "off" position, the scooter will not operate.
-
Battery charge: Check the battery level of your mobility scooter. Ensure that the batteries are fully charged. If they are not, connect the scooter to the charger and allow it to charge for the recommended time (typically 3-4 hours). Insufficient battery charge can cause the scooter to not work or have reduced performance.
-
Inspect for damaged wiring: Examine the wiring of the scooter, particularly in pinch-point locations where wires may be vulnerable. Look for any signs of damaged or frayed wires. Damaged wiring can lead to electrical issues and may prevent the scooter from functioning properly.
If you have gone through these troubleshooting steps and the scooter still does not work, or if you identify any wiring issues, it is recommended to contact our customer support team or seek assistance from a qualified technician. They will be able to provide further guidance and help resolve the issue.
When receiving a scooter frame replacement, there are certain items you should keep from the previous unit. These items include:
-
Seat: Keep the seat from the old unit. The seat is typically compatible with the new frame and can be transferred over to the replacement frame.
-
Batteries: Retain the batteries from the previous unit, as they are not typically included with the replacement frame. Ensure that the batteries are in good condition and compatible with the new frame.
-
Charger: Keep the charger that was originally provided with your scooter. The charger is a separate component and can be used to charge the batteries regardless of the frame replacement.
-
Bag or accessories: If your scooter came with a bag or any other accessories, these can be kept and attached to the new frame.
It's important to note that the specific components to keep may vary depending on the scooter model and manufacturer. Always refer to the manufacturer's instructions or contact their customer support for precise information on the replacement process and which parts to retain.
When replacing the frame, it is advisable to seek assistance from a qualified technician or follow the manufacturer's guidelines for a proper and safe installation. They will be able to guide you through the process and ensure that all necessary components are transferred correctly.
Please remember to dispose of the old frame responsibly or follow any recycling or disposal guidelines provided by the manufacturer or local regulations.
The round black part on the left handlebar of your scooter is a standard bicycle bell. Its purpose is to alert pedestrians or other individuals of your presence and to ensure safer navigation in shared spaces.
In the event that the bell is not working as intended, you can try adjusting it by carefully pulling it up and away from the handlebars to loosen it. However, please exercise caution when doing so. If pulled too forcefully, the bell may come off, but don't worry as it can easily be reattached without the need for any tools. Simply align the bell properly and push it back onto the handlebars until it clicks into place.
By loosening the bell slightly, you should be able to restore its functionality and make it ring again when pressed. This adjustment will allow you to effectively use the bell to signal your presence to others while riding your scooter.
If you encounter any issues with the bell or have further questions regarding its operation, feel free to reach out to our customer support team for additional guidance and assistance.
Reels
If the cord reel is not retracting, it is possible that the spring inside the reel has lost all tension or may have broken. In such cases, it is typically not safe or advisable to open enclosed reels for repair. Opening an enclosed reel can be challenging and may require specialized tools or expertise.
To resolve this issue, it is recommended to replace the entire cord reel. By replacing the reel, you can ensure that the retracting mechanism is functioning correctly and restore proper functionality to the cord reel.
If you are still within the warranty period, please reach out to our customer support team as they will assist you in obtaining a replacement unit.
Utility Cart
-
SuperHandy GUO055: This model is a 48V 2Ah Li-Ion cart that initially comes with one battery. However, it has a slot for two batteries, allowing users to switch between them for extended use. It is also compatible with an extended 4Ah model of the battery. This cart is designed for a maximum weight capacity of 500lbs.
-
SuperHandy GUO095: Similar to the GUO055, this model is a 48V 2Ah Li-Ion cart. However, it includes an additional castor wheel, providing enhanced maneuverability. It is rated for a higher weight capacity of 660lbs, making it suitable for heavier loads compared to the GUO055 model.
-
Landworks GUO026: This model is also a 48V Li-Ion cart from Landworks, which shares similar features and specifications as the SuperHandy GUO055. It is designed for a weight capacity of up to 500lbs.
-
Landworks GUO010: Unlike the previous models, this cart utilizes a 48V 7Ah Lead Acid battery (AGM). The battery is sealed and not intended to be removed unless for replacement purposes. It charges externally using the included charger and adapter. This model is designed for a maximum weight capacity of up to the specified limit.
These variations in the Utility Cart models cater to different preferences and requirements. Factors such as battery type, weight capacity, and additional features like castor wheels differentiate the models. It's essential to select the model that best suits your specific needs and intended applications.
For more detailed information and specific specifications on each model, it is recommended to refer to the product descriptions or reach out to our customer support team for further assistance. They will be able to provide you with precise information tailored to the respective Utility Cart model you are interested in.
Yes, the Utility Cart can be manually pushed, allowing for some degree of movement. However, it's important to note that you may encounter significant resistance when trying to push it manually. The cart is primarily designed to be powered and propelled by its motorized function, such as an electric motor or other means of propulsion.
If your unit is experiencing the issue of only moving in one direction, either forward or backward, but not both, the likely cause is a malfunctioning or faulty direction control panel. The direction control panel is responsible for managing the movement and switching between forward and backward directions.
To resolve this issue, it is recommended to replace the direction control panel. This involves obtaining a new, functioning control panel that is compatible with your specific unit model. The replacement process typically requires some technical knowledge or assistance, especially if it involves disassembling and reassembling components of the unit.
It is advisable to consult the user manual of your unit or seek professional help from a certified technician familiar with your particular device. They can diagnose the exact problem, provide guidance on obtaining the correct replacement part, and assist with the installation to ensure proper functionality.
Remember, attempting repairs or replacements without proper knowledge and expertise may further damage the unit or void any existing warranties. Seeking professional assistance is recommended to ensure the problem is effectively resolved and the unit can move in both forward and backward directions as intended.
Please reach out to Customer Support for further assistance.
The issue you're experiencing with your utility cart could be related to a faulty drive axle. The drive axle is a critical component responsible for transferring power to the wheels and enabling smooth movement. If the drive axle is damaged or worn out, it can result in the cart stopping and going intermittently.
To resolve this issue, it is recommended to replace the drive axle. Replacing the drive axle will ensure that power is consistently transmitted to the wheels, allowing for consistent and uninterrupted movement of the utility cart.
To obtain a replacement drive axle, please contact our customer support team or refer to the manufacturer's customer support resources. They will be able to assist you in identifying the correct replacement part and provide guidance on the replacement process.
If your utility cart is not moving and the battery box lights up, but the throttle charge indicator does not, the issue may lie with the throttle indicator, which includes the switch and speed controller. In this case, it is recommended to replace the throttle indicator assembly to address the problem. The throttle indicator is responsible for interpreting the throttle input and transmitting the appropriate signals to the motor.
If replacing the throttle indicator does not resolve the issue, the next possible cause could be a faulty motor driver. The motor driver controls the power sent to the motor and ensures smooth operation. If the motor driver is faulty, it can result in the cart not moving. In such cases, replacing the motor driver may be necessary.
If you have any additional questions or concerns, please feel free to reach out to our customer support team for further assistance.
While it is not advised to use the utility cart at the beach due to the potential for sand to damage the unit, some customers have reported using it without issue on the beach. However, it's important to consider that beach conditions can vary, and sand can be abrasive and cause damage to the cart's components.
Here are a few factors to consider when deciding to use a utility cart at the beach:
-
Sand and abrasive particles: Sand can get into the various moving parts and mechanisms of the cart, potentially causing damage or affecting its performance. It may lead to issues such as jammed wheels, clogged mechanisms, or increased wear and tear.
-
Corrosion and rust: Exposure to sand, saltwater, and moisture can accelerate corrosion and rust on metal parts of the utility cart, leading to potential long-term damage.
-
Terrain and stability: Beaches often have uneven and soft terrain, which can pose challenges for a utility cart. The cart may struggle to navigate through the sand, resulting in reduced stability and potential tipping hazards.
Given these considerations, it is generally recommended to avoid using a utility cart at the beach to ensure its longevity and optimal performance. If you require a cart specifically for beach use, you may want to explore options designed specifically for that purpose, such as beach carts or wagons that are built to withstand sand and beach conditions.
No, the utility cart does not typically come equipped with a braking system. Utility carts are generally designed for ease of use and maneuverability in various settings. They are often used for transporting items over shorter distances or on relatively flat surfaces.
Unfortunately not, this is something that must be purchased separately. You can Buy that Here
The utility cart's battery compartments typically feature two switches—a black switch and a red switch. Here's what each switch is used for:
-
Black switch: The black switch is used to determine which battery to draw power from. If the utility cart is equipped with multiple batteries or battery slots, the black switch allows you to select the specific battery from which the cart will draw its power. This switch enables you to control the power source and potentially extend the runtime of the cart by using one battery at a time.
-
Red switch: The red switch is the power switch. It serves as the main on/off switch for the utility cart. When the red switch is turned on, it allows the cart's electrical system to receive power from the selected battery (as determined by the black switch). When the red switch is turned off, the cart's electrical system is disconnected from the battery, effectively shutting down the cart.
It's important to follow the proper sequence when using these switches. Typically, you would first select the desired battery using the black switch and then turn on the red power switch to activate the utility cart.
This only applies to 48V models (GUO055, GUO095, and GUO026)
Replacement Parts
Please submit a PARTS REQUEST or visit out parts website HERE
General
If your self-propelled item is not moving despite the motor humming and the axle spinning, a possible cause for this issue could be missing keys from the wheels. The keys play a crucial role in transmitting power from the axle to the wheels, allowing for movement. If the keys are missing or damaged, the power transfer may be disrupted, resulting in no movement.
To resolve this problem, follow these steps:
1. Locate the wheel keys: Consult the owner's manual or examine the wheels to locate the keyways and check if the keys are missing.
2. Obtain replacement keys: Contact the manufacturer or a local authorized dealer to acquire replacement keys specifically designed for your self-propelled item. Provide them with the make, model, and serial number of your equipment to ensure you get the correct keys.
3. Install the replacement keys: Once you have the replacement keys, insert them into the keyways on the axle and align them with the keyways on the wheels. Ensure they fit securely and engage properly.
4. Test the self-propelled function: After installing the replacement keys, test the self-propelled feature by engaging it and checking if the item moves correctly. If the motor hums, the axle spins, and the wheels now have proper traction, the issue should be resolved.
If the problem persists even after replacing the keys, it is recommended to consult a qualified technician or the manufacturer's customer support for further assistance.
To ensure proper functionality and safety, it is essential to keep the power button pressed at all times while slicing with the meat slicer. The safety switch, typically activated by pressing and holding it, is designed to prevent accidental operation or injuries.
Here's what you can do:
-
Safety switch operation: Make sure you are aware of how the safety switch on your meat slicer works. Check the user manual or operating instructions to understand the correct procedure for using the slicer safely.
-
Press and hold the power button: Before engaging the slicer blade, press and hold the power button while simultaneously holding the safety switch. This action will allow continuous power supply to the slicer motor while preventing it from shutting off when you release the safety switch.
-
Maintain constant pressure: While slicing, ensure that you maintain constant pressure on the power button, keeping it pressed throughout the slicing process. This will ensure uninterrupted operation and prevent the slicer from stopping abruptly.
-
Safety precautions: Always follow safety guidelines while operating the meat slicer. Use the appropriate safety equipment, such as cut-resistant gloves, and maintain a safe distance from the blade during operation.
If you have followed these steps and the issue persists, it is recommended to consult the user manual, contact the manufacturer's customer support, or seek assistance from a professional technician experienced in meat slicer repairs.
Oil Pumps
To determine the compatible extension tube for your oil pump, you can refer to the following information:
-
Extension Tube SKU: ET10000-F
- Compatible SKU's: 1701034, 1701031G, GUL002/1701004, GUL003/1701054, GUL001/1701051G
-
Extension Tube SKU: ET20670
- Compatible SKU: 17130503
-
Extension Tube SKU: ET20920
- Compatible SKU: 17130503
These extension tubes are designed to work with specific oil pump models or configurations. The SKU numbers provided are unique identifiers for the extension tubes, and the corresponding compatible SKU numbers indicate the oil pump models or parts that can be used in conjunction with each extension tube.
To ensure compatibility and proper fit, it is important to match the SKU number of the extension tube with the SKU numbers of the oil pump or associated parts. You can refer to the documentation or product specifications of your oil pump or consult with the manufacturer or supplier to confirm the appropriate extension tube SKU for your specific oil pump model.
By selecting the correct extension tube based on the provided SKU information, you can ensure a proper fit and compatibility with your oil pump, allowing for efficient and effective operation.
Snow Thrower
To assemble your snow thrower, please follow these steps:
-
Remove the cap from the lower pole: Start by locating the cap at the lower end of the pole. Remove the cap by unscrewing or pulling it off, depending on the specific design of your snow thrower.
-
Snap the parts in place: Take the parts that need to be attached and align them with the corresponding connection points on the snow thrower. In most cases, these parts will snap or slide into place.
-
Ensure secure attachment: Once the parts are aligned, apply gentle pressure or push them firmly until they are securely in place. Double-check that all connections are tight and properly seated.
-
Verify assembly completion: Review the instruction manual or user guide provided with your snow thrower to confirm that you have completed all necessary assembly steps. Ensure that there are no remaining components or attachments that need to be added.
It is important to note that the specific assembly process may vary depending on the make and model of your snow thrower. Always refer to the manufacturer's instructions and guidelines provided in the user manual for accurate information on assembling your specific snow thrower model.
If you encounter any difficulties during assembly or have further questions, please reach out to our customer support team or refer to the manufacturer's customer support resources for assistance.
Some customers may confuse this with the extension provided on the top half of the snow thrower.
-
Adjust the top half of the snow thrower: Look for an extension mechanism on the top half of the snow thrower. This extension allows you to adjust the height and reach of the snow thrower.
-
Loosen the adjustment knob: Locate the adjustment knob or lever near the top half of the snow thrower. Rotate or loosen this knob to release the extension mechanism.
-
Extend the top half of the snow thrower: With the adjustment knob loosened, carefully pull or push the top half of the snow thrower to extend it to your desired height. Make sure to align the sections properly to maintain stability.
-
Adjust to preferred height: Once the top half of the snow thrower is extended, position it to your preferred height for comfortable operation. Ensure that it aligns with your body height and provides adequate leverage.
-
Tighten the adjustment knob: After setting the top half of the snow thrower to the desired height, tighten the adjustment knob or lever to secure the extended position. This will ensure that the snow thrower remains in place during operation.
Winch
In order to unlock you need to turn the unlock on the side of the item along with making sure there is power going to the item for the item to release the lock.
Plate Compactor
If your plate compactor is not working as expected, the issue might be that the exciter is locked up, which can be caused by a faulty bearing. Here are the steps to address this problem:
-
Replace the bearing: To resolve the locked-up exciter issue, it is necessary to replace the bearing. The bearing is a crucial component that allows the exciter to rotate smoothly. By replacing the faulty bearing, you should be able to restore proper function to the plate compactor.
-
Check for part availability: Verify if the replacement bearing is readily available. If it is in stock, you can order the bearing and proceed with the replacement. However, if the bearing is not available, you may need to consider an alternative solution.
-
Replace the bottom plate: If the required bearing is not available, an alternative option is to replace the bottom plate of the plate compactor. This can be done as a substitute for fixing the locked-up exciter issue caused by the faulty bearing. By replacing the bottom plate, you may be able to restore the functionality of the plate compactor without relying on the specific bearing replacement.
It is important to note that replacing the bearing or the bottom plate of a plate compactor requires technical expertise and knowledge. If you are not familiar with the process or unsure of how to proceed, it is recommended to consult a qualified technician or reach out to the manufacturer's customer support for further assistance.
Augers
-
Verify battery connection: Ensure that the battery is properly inserted into the auger head and securely connected. Make sure there is no debris or corrosion interfering with the battery terminals.
-
Check battery condition: If the battery is fully charged but the auger head still doesn't work, try using the battery in another compatible device, if possible. This will help determine if the issue lies with the battery itself or the auger head.
-
Inspect charging equipment: If your cordless auger head comes with a charging unit, ensure that it is functioning correctly. Check for any loose connections, damaged cables, or indicators that might indicate a charging issue.
-
Contact customer support: Reach out to the manufacturer's customer support for further assistance. They may provide specific troubleshooting steps tailored to your cordless auger head model or offer suggestions based on common issues reported by other users.
-
Seek professional repair: If all troubleshooting attempts fail to resolve the problem, consider taking your cordless auger head to a professional repair service or an authorized service center recommended by the manufacturer. They have the expertise to diagnose and repair more complex issues.
Remember, it's important to follow safety precautions and avoid attempting any repairs or modifications that may void the warranty or cause further damage. Consulting the manufacturer's customer support or seeking professional assistance is always advisable when encountering difficulties with cordless power tools.
Trailer Jack
If your trailer jack is not functioning properly, it may be related to the wiring connection between the trailer and your vehicle. Here's what you can do to troubleshoot the issue:
-
Check the wiring diagram: Refer to the wiring diagram provided below to understand the proper alignment of the hot and ground wires on the 7-point connector. This diagram will help you identify the correct wiring configuration for your trailer jack.
-
Compare with the vehicle connector: Inspect the 7-point connector on your vehicle and ensure that the hot and ground wires are aligned correctly. Compare the wiring in your vehicle's connector with the diagram to verify if they match up.
-
Realign the wires: If you find that the wires in the trailer's connector do not line up correctly with the vehicle's connector, you may need to make adjustments. Carefully remove the cover of the trailer jack's connector and move the wire to the correct location as indicated by the wiring diagram. This will ensure that the wiring engages properly with the vehicle.
By aligning the hot and ground wires correctly and making any necessary adjustments, you should be able to resolve the issue with your trailer jack not working.
If you continue to experience difficulties with your trailer jack or if the issue persists after following these steps, we recommend contacting our customer support team or seeking assistance from a professional trailer technician.
Tugger
The duration of operation for the Tugger Scooter depends on several factors such as the load being towed and the speed at which it is operated. Here are the estimated run times for the Tugger Scooter under specific conditions:
-
At full charge and no load: When the Tugger Scooter is fully charged and operated without any load being towed, it can run continuously for approximately 1 hour and 50 minutes at high speed. This duration provides an estimate of the scooter's battery life when used under optimal conditions without any additional weight.
-
At full charge and towing a load of 1320 lbs (600 kg): When the Tugger Scooter is fully charged and used to tow a load weighing up to 1320 lbs (600 kg), it can run continuously for approximately 1 hour at high speed. It's important to note that towing heavier loads may decrease the overall run time due to increased power requirements.
Please keep in mind that these run times are approximate and may vary based on factors such as terrain, temperature, battery condition, and user behavior. Additionally, operating the Tugger Scooter at lower speeds or with lighter loads may extend the run time.
Engine
For a 4-stroke engine:
When using a 4-stroke engine, it is recommended to use ethanol-free gasoline, if available. Ethanol-free gas helps prevent potential issues caused by the ethanol content in regular gasoline, such as fuel system corrosion and damage to engine components. However, if ethanol-free gas is not readily accessible, you can use gasoline with up to 10% ethanol content (E10). Here are the recommended guidelines:
- Fuel type: Use unleaded gasoline.
- Ethanol content: Ideally, choose ethanol-free gasoline. If not available, use gasoline with up to 10% ethanol (E10).
- Octane rating: Use at least 87 octane gasoline. This rating indicates the fuel's resistance to knocking or pre-ignition. Using gasoline with a higher octane rating than the minimum requirement is generally fine, but higher octane fuel does not necessarily enhance engine performance.
It's important to note that you should always consult the specific manufacturer's recommendations for your 4-stroke engine, as fuel requirements may vary slightly between models.
For a 2-stroke engine:
When using a 2-stroke engine, it is crucial to follow the correct fuel mixture to ensure proper lubrication and performance. Here are the recommended guidelines:
- Fuel type: Use a 50:1 premix fuel and oil mixture. This means mixing 2.6 ounces (77 ml) of 2-stroke engine oil per 1 gallon (3.8 liters) of gasoline. Use a high-quality 2-stroke oil recommended by the engine manufacturer.
- Fuel octane rating: Use at least 87 octane gasoline. As with the 4-stroke engine, the octane rating indicates the fuel's resistance to knocking or pre-ignition.
Ensure that you mix the fuel and oil thoroughly before adding it to the 2-stroke engine's fuel tank. Using the correct fuel mixture is vital to prevent engine damage and ensure optimal performance.
Remember to always consult the engine manufacturer's recommendations and refer to the owner's manual for the specific fuel requirements of your equipment, as they may vary depending on the make and model.
The PTO (Power Take-Off) shaft rotates in a specific direction depending on the application and the specific equipment or machinery being used. While the counter-clockwise rotation is a common configuration, it's essential to note that the direction of rotation can vary.
To determine the exact rotation direction of the PTO shaft, you should refer to the equipment's user manual or consult the manufacturer's specifications. The user manual typically provides detailed information on the PTO shaft's rotation direction specific to your equipment model.
Additionally, when examining the PTO shaft, you can observe the markings or arrows on the shaft itself or the related components. These indicators often provide visual cues to help determine the direction of rotation.
It's crucial to understand the correct rotation direction to ensure proper coupling and operation with other equipment or machinery that connects to the PTO shaft. Incorrectly connecting equipment to the PTO shaft with mismatched rotation directions can result in malfunctions, inefficiency, or damage to the equipment.
Therefore, when in doubt, always consult the equipment's user manual or contact the manufacturer directly for precise information regarding the rotation direction of the PTO shaft for your specific equipment.
Replace motor ( GUT031 )
Troubleshooting Steps:
-
Check the fuel level: Ensure that there is enough fuel in the tank. If the fuel level is low, refill it with fresh gasoline.
-
Check the spark plug: Inspect the spark plug to ensure it is clean and in good condition. If it's dirty or worn out, clean or replace it as necessary.
-
Check the air filter: A clogged or dirty air filter can restrict airflow to the engine and prevent it from starting. Remove the air filter and clean or replace it if necessary.
-
Check the oil level: Ensure that the engine has sufficient oil. Low oil levels can trigger the oil pressure switch and prevent the engine from starting. Add oil if needed, following the manufacturer's guidelines.
-
Inspect the spark plug wire: Make sure the spark plug wire is securely connected to both the spark plug and the ignition coil. A loose or damaged wire can disrupt the ignition system and prevent the engine from starting.
-
Test the ignition system: If the above steps don't resolve the issue, you may need to test the ignition system components, such as the ignition coil and magneto, using a spark tester. Consult the engine's manual or seek professional assistance for this step.
-
Disconnect the oil pressure switch wire: As previously mentioned, a faulty oil pressure switch can prevent the engine from starting. Disconnect the yellow wire connected to the oil pressure switch (located to the right of the pull cord) and see if the engine starts. However, remember to manually check the oil levels before every other use if you choose to operate the engine with the wire disconnected.
If the troubleshooting steps above do not resolve the issue, it is recommended to consult a qualified technician or the manufacturer's customer support for further assistance.